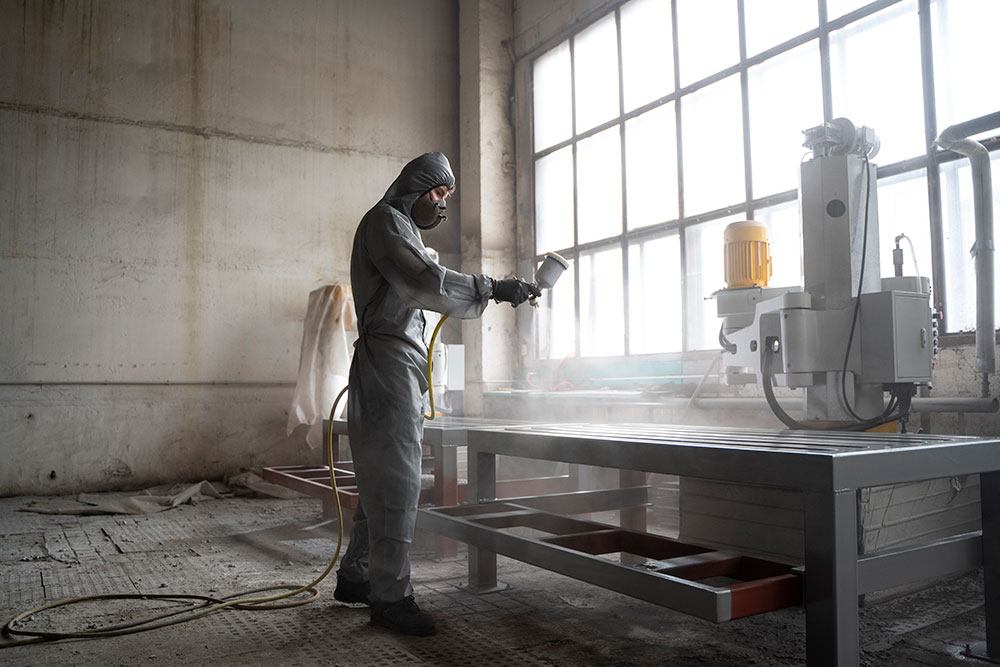
Dust produced during the manufacturing and processing of food products creates a number of significant challenges. Dust particles varies in size, and some are so fine that they are not visible to the naked eye. These particles often become airborne, which can threaten worker health and cause incidents. Cross-contamination is another serious concern in food processing industry. Common dust in food industry is generated by processing of cereal ingredients, spices, feed and raw grain agricultural products, flour, corn starch, sugar, and flavoring additives.
Without an industrial dust collection system, particles will settle on the surface of floor, equipment and other objects where they are difficult to remove. Traditional methods of cleaning like mops, compressed air and standard vacuum cleaners cannot effectively collect all of the contaminant-containing dust from the processing area. Even worse, they tend to kick the dust up into the air, redistributing it to other parts of the plant and contaminating food products.
Installation of a well-designed industrial dust collection system prevents airborne dust from building up in the work environment, on electrical equipment and on other areas where dust can accumulate, such as false ceilings.
In the food processing and chemical industry, the finished or semi-finished products are often crushed, and the crushed material is recycled or retreated. As the crusher is operated at a high speed with sharp cutters, large amount of airborne particles can spread in the work environment, and would ultimately affect the health of employees. The airborne dust can also hurt a facility’s aesthetics.
In view of this kind of dust, it is necessary to follow up the actual crushing amount and dust flying direction for reasonable design and selection of suction hood and subsequently the industrial dust collector.
The feeding process involves the conversion of diverse raw food ingredients into a single, homogenized form of feed, such as mash, pellet, and crumbles, etc. During this process, the fine dust coming out travels through the worker’s breathing zone and into the rest of the facility. Exposure to such dust can be hazardous to worker’s health.
Similarly, during the batch mixing process of food production, when the raw materials are poured together for the mixing process, a large amount of airborne dust is generated, which gradually spread in the workshop environment. Furthermore, if the dust is flammable and explosive, it can also threaten the lives of employees.
In order to handle this kind of dust, it is necessary to reasonably design the size and installation mode of the suction hood, and the industrial dust collection system should be carefully calculated and selected.
The spray drying process involves the atomization of liquid feed into a spray of droplets using high pressure. At the same time, dry high-temperature gas is introduced to quickly dry the mist preparation into a powder and settle on the bottom of the machine. The inside of the dryer is a closed environment, and the amount of air injected needs to be discharged in time to ensure that the pressure inside the dryer is balanced.
The exhaust gas contains fluttering powder and a small amount of water, which needs to be filtered through an industrial dust collector before being discharged into the air. An industrial dust collector should be selected based on the dust properties.
Weighing and packaging processes are another major sources of dust generation during food processing. During these processes, a significant amount of airborne dust is generated which is not only hazardous to human health but can also accumulate on equipment and electronics, causing them to malfunction or fail.
The dust produced during weighing and packaging is a kind of floating dust. For this kind of dust, it is necessary to combine the operating habits of employees, the size of material inlet, and the size of dust volume as a reference to design and select an industrial dust collector.
The dust deposited on the ground during food processing belongs to static dust. High negative pressure industrial vacuum cleaners can be used to extract such kind of dust. Industrial vacuum cleaners can have different configurations such as manual dust removal, manual dust vibration, and pulse back blowing and can be opted depending upon the requirements. In addition, the industrial vacuum cleaner with 380V voltage or 220V can be selected according to the customer’s site requirements.
Food processing can produce serious amount of dust which can have harmful effects on both, the employees and the equipment. While most food processing dust may appear less harmful, prolonged exposure to them can be dangerous. An industrial dust collector can capture the harmful dust media before it can accumulate in the ambient air.
Villo Vacuum, the leading industrial dust collector manufacturer, provides comprehensive solutions to guarantee production safety, product quality employee health during the production process. In the past few years, Villo Vacuum has been committed to provide a variety of industrial dust collection solutions worldwide. We propose the ideal solution by professionally modeling your facility to guarantee the performance.
English
Français
Deutsch
日本語
한국인